For centuries red has been revered–and hard to come by–as a color to dye for. Its scarcity, along with purple, has often made it a color reserved for royalty. But over the centuries some recipes have been developed to achieve a vibrant red. This month we are dyeing some of our wool with cochineal, a red dye developed in South and Central America. This dye was developed from beetles(!) that live on cactus plants. It has been used as the Navajo red made famous in some of the early rugs from the Navajo nation.
The process is not simple. We mordanted our wool. (That means pre-treating it with an oxide solution to help fix the dye so it won’t fade). We had purchased a few ounces of the dried cochineal beetles which we ground in a coffee grinder that we use exclusively for our dyeing. We mixed these powdered beetles with water and simmered the mixture for an hour. We then took our warmed damp mordanted wool skeins and simmered them in the dye bath.
Some of the skeins we had already dyed yellow of blue, so we were overdyeing them to see what colors we might get.


Here is the result of our adventure.

As usual we had a few surprises but were very impressed with our results.
We now have the following tapestry wool for each of the members. The first photo, from left to right, shows wool dyed in weld (top), dyed in osage orange (bottom). The next two skeins are indigo dyed dipped three or four times (top) and dipped one time (bottom). The third set of skeins are the weld and osage orange skeins over-dyed with one dip in indigo and the last two skeins were over-dyed three or four times in indigo.
The second photo is weld over-dyed with cochineal and osage orange over-dyed with cochineal.
The third photo is indigo dipped four times and over-dyed with cochineal.



In 2012 I visited two Zapotec weavers, Jaime and Joey, who lived in the Central Valley. Jaime’s family, originally from Mexico, had been weavers for four generations. Hanging on the front porch were a number of cactus pads, which Jaime’s father had gathered from the desert in Southern California. The cactus was home to cochineal beetles who protect themselves from the desert heat by surrounding themselves with a white “insulation” which they produce somehow.
Jaime crushed one of these “cocoons” to show me the red produced by the beetles, which are dried before being used. (They literally die for dye!)
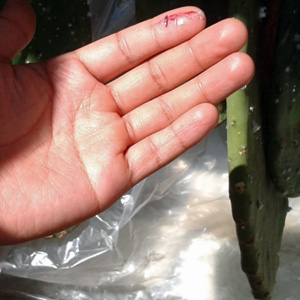
We also were intrigued to see Sharolene’s new tiny spinning “wheel”. This little portable device is an electric spinner that can run off a battery, is speedy and versatile, and makes almost no noise. See more about it here.
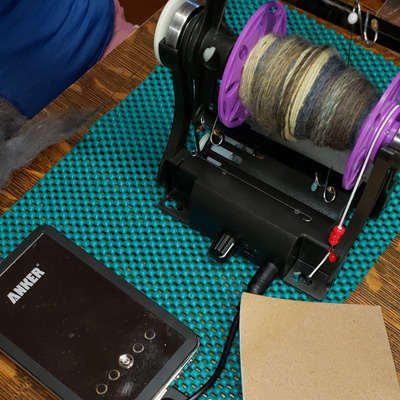